In the high-demanding field of industrial applications, ensuring the reliable functionality of equipment in high-temperature environments is crucial. A particular game-changer in overcoming these challenges is the slip ring. This guide presents a detailed look into the fundamental role of slip rings in industrial high-temperature applications, the relevant selection factors to consider, their benefits, and answers to commonly asked questions.
Table of Contents
- Importance of Slip Rings for Industrial High-Temperature Applications
- Slip Rings Are Mainly Used in Industrial High-Temperature Applications Where?
- Types of Slip Rings for Industrial High-Temperature Applications
- Factors to Consider in Selecting Slip Rings for Industrial High-Temperature Applications
- Benefits of Slip Rings for Industrial High-Temperature Applications
- Frequently Asked Questions
Importance of Slip Rings for Industrial High-Temperature Applications
Slip rings serve as an electrical connector designed to transfer power or data from a stationary component to a rotating component. Their centrality in industrial high-temperature applications cannot be overemphasized primarily due to their unique ability to withstand extreme temperatures and maintain consistent high operational efficiencies simultaneously.
Slip Rings Are Mainly Used in Industrial High-Temperature Applications Where?
Slip rings are pivotal in industrial high-temperature applications where seamless power transmission and persistent signal integrity are a prerequisite for unbroken operation, even under high ambient temperatures. They are typically employed in machines or devices that incorporate a rotating part that requires electrical power or needs to transfer signals.
For instance, the application includes but is not limited to industrial furnaces, where temperature regulation is critical and rotation is typically involved in shaping or tempering processes.
Similarly, in wind turbines, which are often exposed to temperature variations, slip rings ensure power supply to the rotating blades and transmit data regarding the blade performance and weather conditions. Other key high-temperature applications encompass molding machines, downhole drilling rigs, medical CT machines, and even food processing machines that require frequent heat treatments or pasteurization.
The choice of a slip ring, in essence, has a direct impact on the operational efficiency of these devices. Hence, a deeper understanding of their types, their selection parameters, and potential benefits can be instrumental in optimizing application performance and promoting longevity, even in the challenging environment of high-temperature industrial applications.
Types of Slip Rings for Industrial High-Temperature Applications
Different types of slip rings have been crafted to suit specific high-temperature industrial applications. Broadly, these can be categorized into:
High-temperature Slip Rings: These are specially engineered to continue transmitting power and signals with negligible losses, even in conditions reaching 200°C. They are typically made with specific materials and feature designs that allow for efficient heat dissipation, preventing any impact on performance due to temperature rise.
Furnace Slip Rings: As their name signifies, these are used in furnaces and other high-temperature industrial setups. They possess superior high-temperature tolerance and demonstrate excellent insulation capability, thus being able to maintain a steady electrical connection in persistent high-temperature environments.
High-Speed Slip Rings: These slip rings are designed for applications that couple high rotational speed with high operating temperature. They are built with meticulous precision for low contact resistance, which allows for faster data transmission and less heat generation, making them ideal for applications like wind turbines or aerospace equipment.
Through Hole Slip Rings: Also known as hollow shaft slip rings, these are primarily designed for applications where a clear passage is required through the center. They can handle high temperatures and are customizable in terms of size and capacity to fit a range of industrial applications, such as rotary tables, packaging machines, and more.
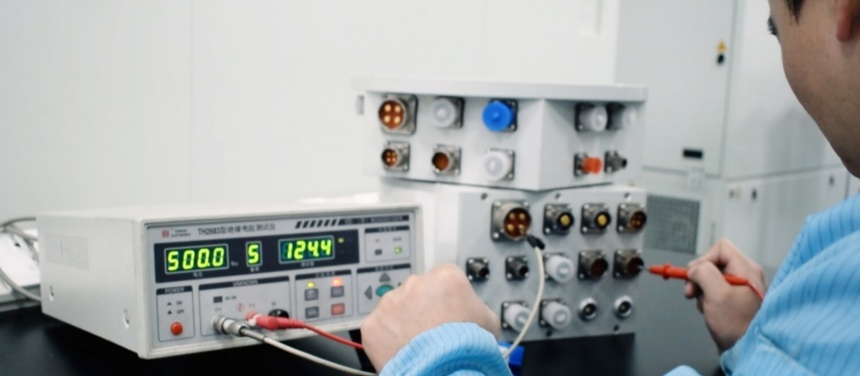
Each type of slip ring listed above serves a specific purpose and is better suited to various operational environments than the others. The choice of the slip ring should be heavily influenced by the intended application requirements, the temperature and pressure conditions, as well as operational expectations.
Factors to Consider in Selecting Slip Rings for Industrial High-Temperature Applications
Making the right choice when selecting slip rings for high-temperature industrial applications requires a thoughtful consideration of several key factors including:
Temperature Tolerance: A crucial factor is the slip ring’s ability to withstand high temperatures. Typically, you’d want a slip ring that can effectively operate under temperatures up to 200°C. This is particularly significant in applications like furnaces and other high-heat processes where temperatures could go beyond normal levels.
Pressure Tolerance: Industrial applications often function under high pressure, hence the need for a slip ring that can withstand pressures up to 25,000 psi or 1700 Bar, maintain operational integrity, and prevent pressure-related abnormalities or damages.
Size Customization: The size of the slip ring should also be considered. The inner bore and outer diameter of the slip ring need to be appropriate for the specific application it is intended for.
Customizable slip rings are favored in this regard as they enable fitting into various machine assemblies without interfering with the machine layout or operation.
Contact Resistance: High contact resistance in a slip ring directly correlates with higher energy loss and greater heat generation, which isn’t beneficial in a high-temperature environment.
Hence, it is important to select a slip ring with low contact resistance – this not only boosts the efficiency of electrical power transmission but also reduces heat, thereby providing more durability and longevity.
Taking into account these factors will not only ensure the proper functioning of the slip ring in your application but also enhance the overall system performance and its lifespan in demanding high-temperature conditions.
Benefits of Slip Rings for Industrial High-Temperature Applications
The use of slip rings in industrial high-temperature applications presents numerous benefits, primarily contributing to enhanced performance, reduced downtime, and cost efficiency:
Reduces Wear and Tear: One of the significant benefits of slip rings is their ability to reduce stress on the system. Unlike traditional rotating mechanisms that may struggle with wire twists and tension, slip rings bypass this by allowing the free rotation of parts – thereby drastically reducing wear and tear.
Decreases Maintenance Time and Cost: Given their ability to reduce friction, decrease wear, and resist high temperatures, slip rings inherently require less replacement and repair – directly translating into decreased downtime for maintenance and resultant cost savings.
Increases Operational Efficiency: Slip rings with low contact resistance are designed to maximize power transmission efficiently. This means less energy loss, lower heat generation, and, ultimately, enhanced overall operational efficiency for the system.
Versatility: A significant benefit of slip rings is their adaptability. They can be customized to fit a range of sizes and application-specific requirements, thereby making them an extremely versatile solution for diverse high-temperature industrial applications.
By incorporating slip rings into high-temperature industrial applications, organizations can optimize their processes, elevate efficiency, safeguard their equipment’s longevity, and accumulate substantial savings over time.
Frequently Asked Questions
At this juncture, it’s fitting to address some typical questions related to slip rings in high-temperature industrial applications:
Q: Can all slip rings be customized?
A: Not all but most manufacturers offer customization options for outer and inner dimensions.
Q: What maintenance activities do slip rings require?
A: Maintenance activities are largely dependent on the manufacturer’s instructions. However, regular inspection for wear and tear is recommended.
Q: Are there any safety precautions when using slip rings?
A: Yes, safety precautions include avoiding overloading, keeping the operating conditions within the slip ring’s specified metrics (such as temperature and pressure), and regular maintenance.
Q: What happens if a slip ring’s temperature exceeds its specified limit?
A: If a slip ring is subjected to higher temperatures than its design limit, it might lead to degradation of insulation, increased electrical resistance resulting in power loss, and premature wear of the contacts. In worst-case scenarios, overheating could cause a system failure.
Q: How long does a slip ring typically last in a high-temperature industrial application?
A: The lifespan of a slip ring hinges on several factors such as the quality of the slip ring, the environmental conditions, the operational load, and the schedule of maintenance. However, with proper use and regular maintenance, a quality slip ring should last for several years. It’s advisable to consult the manufacturer’s specification or a technical expert for detailed information.
These FAQs are designed to give a broad understanding of slip rings in high-temperature industrial applications. However, for application-specific concerns, it’s always best to reach out to the slip ring manufacturer or a qualified technician.
To wrap up, the right choice and utilization of slip rings in high-temperature industrial applications can substantially enhance operational efficiency, mitigate system wear, and, consequently, reduce maintenance costs. The fundamental understanding of the importance, distinctive features, benefits, and frequently asked questions about these devices will aid enormously in making informed decisions while sourcing and integrating a slip ring into your high-temperature industrial setup.
Request information on our slip ring warranty and support.