Metal slip rings find their utility in a myriad of applications ranging from wind turbines to electrical generators. Understanding them better equips us to utilize them optimally. This article serves as a one-stop guide to all things related to metal slip rings.
Introduction to Metal Slip Rings
Slip rings play a vital role in systems where electricity or data transmission from a stationary component to a rotating component is required. A metal slip ring, specifically, is a type of slip ring made up of conductive metal that allows this crucial transfer. The primary function of these metal slip rings is to ensure uninterrupted electrical conductivity between stationary and rotating parts without restricting the latter’s movement, which is why they are also often referred to as rotary electrical joints.
Metal slip rings are typically constructed with a conducive metal ring and a brush. The brush, made from copper or another conductive metal, slides over the rotating metal ring. Through this, electrical impulse or power precisely moves from the stationary structure (connected to the brush) to the rotating structure (connected to the ring).
Key areas of application for metal slip rings are extensive, given their inherent utility and wide-ranging adaptability. They are used in a multitude of machine designs and automation systems. For instance, you’ll find them in critical areas of the automotive industry, where they are embedded in steering columns to control airbags, sensors, and infotainment systems.
Equally, metal slip rings are pivotal in the functioning of wind turbines. Here, they aid in power and data transmission from the stationary wind turbine tower to the constantly rotating nacelle. For similar reasons, these components also find active use in the medical field, particularly in CT scan machines where the body part stays static, but the scanner revolves around it. Other areas of application include defense, aerospace, heavy industry, and robotics, to name just a few.
The standard and specialization of metal slip rings one might use depend significantly on the specific application in question. The wide usage sphere is attributable to the fact that these devices come in various shapes, sizes, and even customizations, offering effective solutions for diverse settings. For users and potential users alike, a good grasp of the basics of metal slip rings, their design principles, and their usage can prove invaluable in optimizing their usage and harnessing their tremendous potential in various applications.
Design and Operational Principles of Metal Slip Rings
Components of a Metal Slip Ring and Their Functions
A basic metal slip ring assembly consists of three main components that work in unison to achieve effective and efficient power or data transmission:
- Rotor (Conductive Metal Rings): This forms the central part of the device. Designed to rotate, the rotor’s primary function is to establish electrical contact with the stationary brush while being connected to the rotating machinery part.
- Brush (Conductor): The brush slides over the rotating rings as it rotates, facilitating the transmission of electrical signals or power. It is typically made of metal or graphite and is connected to the stationary part of the machinery.
- Housing (Insulator): The housing, being a non-conductive material, is used to provide an insulating barrier. It supports and protects the other components, ensuring no electrical leakage to the outer side, and preventing any foreign material or human contact from interfering with the operation process.
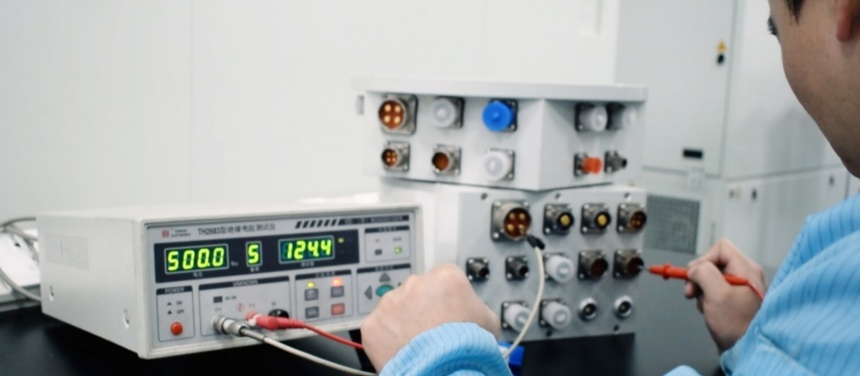
Explanation of How Metal Slip Rings Work
The functional principle of a metal slip ring is based on the simple concept of transferring power or signals from a stationary component to a rotating one. Here’s how it works:
When the system is in operation, the brush, which remains stationary, comes into contact with the rotating metal ring (or rotor). As the rotor turns, the brush maintains its contact, thus establishing an electrical connection between the stationary and rotating parts— this effectively creates a ‘slip’ between the brush and the ring.
Electricity or signals are transmitted through this slip-connection from the stationary part, connected to the brush, to the rotating part connected to the rotor, without hindering the rotation. This ensures continuous and seamless power or signal transmission, irrespective of the rotational speed, which might vary from very slow to very high in different applications.
Due to the metal’s superior conductivity compared to other materials, metal slip rings provide high efficiency, longevity, and reliable performance, making them the preferred choice in various industries and applications. Nevertheless, the material choice, design concepts, and manufacturing precision of the slip ring play a critical role in determining the performance and service lifespan of the metal slip ring assembly.
Understanding these principles of metal slip ring design and operation fosters a better appreciation of their capabilities and allows users to make more informed decisions when selecting, installing, and maintaining these devices.
Types of Metal Slip Rings
Classification Based on Materials Used
Metal slip rings come in various types, mainly distinguished by the type of conductive metal used in their construction. Some common types include:
- Brass Slip Rings: These are frequently used in applications that require a satisfactory balance between cost-effectiveness and operational efficiency. Brass, being resistant to corrosion and having reasonable electrical conductivity, is the material of choice for these slip rings.
- Aluminum Slip Rings: These are lightweight, making them suitable for applications that prioritize weight constraints. Aluminum offers sound electrical conductance coupled with excellent corrosion resistance.
- Silver Slip Rings: Showcasing superior electrical and thermal conductivity, silver slip rings are ideal for high-performance environments. However, they are pricier due to the cost of silver.
- Gold Slip Rings: Used in highly specialized applications, these offer extremely high conductivity and excellent corrosion resistance. Their cost tends to be high due to the value of gold.
Impact of Different Metals on Conductive Performance, Durability, and Cost
The selection of metal significantly influences the performance, durability, and cost of a slip ring:
- Conductive Performance: Metals like silver, gold, and copper provide excellent electrical conductivity, ensuring efficient signal transmission. On the other hand, brass and aluminum, while offering reasonable conductivity, cannot match the performance of silver or gold.
- Durability: Metals like aluminum and brass show great corrosion resistance, contributing to their durability. While Silver and gold are similarly resistant to corrosion, their softness could result in enhanced wear and tear during operation.
- Cost: The cost of material directly affects the overall price of the slip ring – while brass and aluminum are cheaper, high-value metals like gold and silver lead to an expensive slip ring.
Hence, the metal choice varies based on the specific requirements of the application. Silver and gold slip rings might be better for environments needing high-performance transmission or specialized applications, while those made from brass or aluminum may be favorable for cost-effective, everyday applications. It’s essential to understand this interplay between the material selection and the subsequent impact on performances and costs to make an informed decision aligning with the specific requirements.
Criteria for Selecting a Metal Slip Ring
Choosing the right metal slip ring is a pivotal task that requires comprehensive consideration of several factors. One must evaluate these aspects for alignment with their specific system or application requirements to ensure optimal performance and prolonged lifespan. Here are some key aspects to consider:
- Rotational Speed: The rotational speed of your operation directly impacts the selection of a slip ring. While some slip rings are designed to function at high rotational speeds, others might be better suited for low-speed operations. For instance, in applications with high rotational speeds, gold or silver slip rings that exhibit superior conductivity may be more effective.
- Insulation Resistance: The ability to resist electrical leakage is another crucial factor when selecting a slip ring. Higher insulation resistance enhances efficacy and ensures safety. Different metals differ in their insulation resistance properties, so it’s imperative to consider this factor in your specific application.
- Temperature Tolerance: Different metals have varying levels of heat resistance, which affects how well they can perform under high-temperature conditions. For example, copper has a lower melting point compared to aluminum. Hence, if the application deals with high temperatures, materials with higher heat resistance like aluminum are more suitable.
- Durability: As mentioned earlier, the choice of metal can directly impact the durability of the slip ring due to various factors such as corrosion resistance and physical hardness. Evaluating the operational conditions, environmental factors, and expected lifespan of your machinery can aid in making an informed decision.
- Cost: Various factors such as material cost, customization needs, and maintenance expenses contribute to the total cost of ownership of a slip ring. While high-value metals like gold and silver may offer excellent performance, their initial cost can be prohibitive for some. Brass and aluminum slip rings, on the other hand, could provide a more cost-effective solution for less demanding applications.
- Purpose & Environment of Application: The distinct purpose and environment of your application also play a significant role in the selection process. For instance, slip rings used in wet or humid conditions should preferably exhibit higher corrosion resistance. Similarly, slip rings in abrasive environments should be made from materials with high hardness and wear resistance to ensure a longer lifespan.
When selecting a metal slip ring, understanding the operational needs and constraints helps in making a more sophisticated evaluation and arriving at the most suitable choice.
Metal Slip Rings Installation and Usage Tips
How to Install a Metal Slip Ring – A Step-by-Step Guide
Proper installation of metal slip rings is vital for optimal performance and an extended lifespan. Here is a step-by-step guide outlining general installation:
Step 1: Before starting the installation, ensure the environment is clean, free of dust, and has the appropriate temperature.
Step 2: Carefully locate the rotational part of the machine where the rotor of the slip ring will be installed. It must be a part that rotates during operation and carries the electric current or signal.
Step 3: Connect the rotor to the rotating part of the machine. Most slip rings have provisions, like holes for fixing screws, to make the process easy and secure. Ensure that there is a good fit and that the rotor is firmly attached and can spin freely.
Step 4: Similarly, locate and connect the stationary part of the machinery to the brush assembly. The brush holder should be adequately affixed to prevent unnecessary movement that might disrupt the smooth operation of the slip ring.
Step 5: After attaching both parts, verify the placement with a test run. Check that the brush slides smoothly on the rotating part and that it maintains constant, firm contact, without causing excessive friction or wearing out.
Step 6: Do a few complete rotations to ensure that the metal ring rotates uninterrupted. Make sure that the wires are not tangled or loosened during rotation.
Best Practices for Using Metal Slip Rings
As a user, adhering to the following practices can enhance performance and prolong the lifespan of a metal slip ring:
- Regular Inspection: Regular checks on the slip ring’s components are necessary to ensure they’re in good condition. Any signs of wear, corrosion, or dust accumulation should be addressed immediately to prevent further degradation.
- Maintenance & Cleaning: Adequate and regular cleaning will help maintain the slip ring’s performance by preventing dust accumulation that might cause friction and impede conductivity. A non-residue cleaner is typically effective for this purpose.
- Replace Worn-out Parts: If there are signs of excessive wear on components, especially on the brushes or the rotating ring, they should be replaced promptly. Prolonged use of worn-out parts can lead to failures or reduced efficiency.
- Use Correct Stimulus: Ensure that the electrical signals or power inputs do not exceed the specified rating of the slip ring. Overloading can cause excessive heat and potential long-term damage.
- Environmental Control: It’s crucial to have the slip ring installed in a controlled environment shielded from excessive dust, extreme temperatures, or aggressive chemicals. These external factors can lead to higher wear and tear or decreased performance.
Understanding and implementing these best practices can greatly enhance the performance, efficiency, and lifespan of a metal slip ring. Each application might require further specific handling and maintenance practices, so it’s advisable to adhere to the instructions provided by the manufacturer or a professional to get the most out of your metal slip ring.
Common Problems with Metal Slip Rings and Troubleshooting
Despite utmost care, users may occasionally encounter problems with their metal slip rings. However, knowledge of common issues and effective troubleshooting can help maintain the slip rings’ effectiveness and longevity. Here we identify common issues and their respective solutions.
Contact us to learn about our Metal Slip Rings quality assurance.
Issue Diagnosis: Identifying Common Problems
Problem 1: Reduced Electrical Conductivity
Users may often encounter reduced transmission or loss of signals, indicating a decrease in electrical conductivity.
Problem 2: Overheating
Overheating is a common problem with slip rings. If the slip ring becomes excessively hot during operation, it could signify a problem.
Problem 3: High Noise or Vibration
If a slip ring generates an unruly amount of noise or vibration during use, it may indicate a hardware problem.
Problem 4: Rapid Component Wear
If the components, particularly the brushes or the rotating rings, observe rapid wear and tear or corrosion, it can impact the performance and longevity of the device.
Practical Solutions for These Problems
Solution 1: Ensure Regular Cleaning
To address reduced electrical conductivity, regular cleaning is essential. Accumulation of dirt or dust can form a layer over the conductive surface, disrupting its efficiency. Use a non-residue cleaning solution to remove any dirt buildup.
Solution 2: Monitor Electrical Input
Overheating often occurs due to excessive power load. Ensure the input doesn’t exceed the slip ring’s rated current. Reduce the input power if required or ensure efficient heat dissipation mechanisms are in place.
Solution 3: Check Assembly & Installation
Unwanted noise or vibrations usually result from loose or improper installation. Verify that all components are appropriately tightened and aligned. If an issue persists, it may be necessary to check if the brushes or conductive ring is damaged and needs replacement.
Solution 4: Regular Inspection and Prompt Replacement
Quick wearing out of components could be due to sub-optimal operating conditions or inferior material quality. Regular inspection can help identify any abnormal wear. If any component is damaged, it’s crucial to replace it promptly to prevent further issues.
It’s fundamental to remember that the actual problems and their solutions can vary based on the specific metal slip ring type and application. Therefore, always consider the manufacturer’s instructions and consult a professional when necessary.
Maintenance of Metal Slip Rings
Maintenance of metal slip rings is of prime importance to ensure their optimal functionality and to extend their lifespan. Regular maintenance not only helps in efficient performance but mitigates costly downtime due to unexpected breakdowns or faults. Here, we delve into regular maintenance practices suitable for metal slip rings:
- Regular Cleaning: This is the most basic maintenance task suited for metal slip rings. Electrical contacts can gather dust, and grime, or oxidize over time, reducing electrical conductivity and causing wear and tear. A non-residue cleaner is recommended to clean the conductive surfaces without leaving any film or residue that could decrease efficiency.
- Routine Inspection: Manifestations of any potential problem can often be spotted during regular inspections. Key things to monitor include any discoloration on the metal surface (which might suggest heating issues), excessive wear on brushes or rings, and looseness or friction in the components indicating misalignment.
- Lubrication: Certain metal slip rings might benefit from regular lubrication. It might be necessary for applications with high rotational speeds or heavy loads to reduce friction and prevent wear and tear. However, it’s important to use only the recommended lubricants in the correct quantity to prevent any adverse effects.
- Component Replacement: Even with the best maintenance practices, inevitable wear and tear can render certain components less efficient over time. Regular inspection can help you identify the right time to replace them. Brushes, due to their constant contact with the rotating ring, are among the components that might require frequent replacement.
- Avoid Overloading: Overloading the slip ring with electrical signals or power beyond its capacity not only reduces efficiency but also risks permanent damage. To prevent this, ensure that the input does not exceed the stipulated rating of the slip ring.
- Environmental Control: Lastly, controlling the environment in which the slip ring operates can also contribute to maintenance. High levels of dust, corrosive elements, humidity, and extreme temperatures can all affect performance and lifespan.
Keeping these maintenance practices in mind helps preserve the functionality of a metal slip ring. However, maintenance tasks can vary depending on specific types of slip rings and their application. Always refer to the specific maintenance protocols provided by the manufacturer to ensure desired results.
Market Trends and Future Developments in Metal Slip Rings
The metal slip rings market has witnessed significant innovation and development owing to increasing demand in diverse industries like wind power, defense, and heavy machinery, amongst others. Below, we will discuss the latest market trends and foreshadow future developments for this essential technology.
Latest Trends in the Metal Slip Rings Market
- Increasing Demand in Renewable Energy: Metal slip rings play a critical role in wind turbines. They facilitate the transmission of power and signals from the rotating turbine to the static structure. With a global shift towards clean and renewable energy sources, the demand for efficient and durable metal slip rings is on the rise.
- Miniaturization Trend: As numerous industries are demanding compact and efficient devices, manufacturers are working towards the miniaturization of metal slip rings without compromising performance and reliability.
- Focus on Durability and Efficiency: As the applications of metal slip rings become more demanding, there is a growing emphasis on enhancing durability and efficiency. Manufacturers are leveraging advanced materials and manufacturing processes to produce robust metal slip rings capable of withstanding harsh environments.
Future Outlook of Metal Slip Ring Technology
- Integration with Advanced Materials: As technology progresses, manufacturers might look to incorporate advanced materials into their designs to improve electrical conductivity, strength, and temperature resistance.
- Increased Adoption in Robotics: As the field of robotics and automation continues to expand, the utilization of metal slip rings for signal and power transmission in complex robotic systems could see a considerable rise.
- IoT and Remote Monitoring Integration: To keep pace with the digital revolution, future developments in metal slip rings may include integration with Internet of Things (IoT) technology. This will allow for real-time monitoring, prediction of maintenance needs, and overall more efficient operation.
- Environmental Sustainability: With the escalating focus on environmental sustainability, future slip rings might be designed in a way that reduces environmental impact, perhaps through the use of recycled materials or ensuring the rings are at the end of their lifecycle recyclable themselves.
The metal slip rings market remains dynamic, with constant advancements aimed at increasing durability, miniaturizing designs, and excelling in different environmental conditions. With technology progressing rapidly, the metal slip ring industry is expected to keep evolving to meet the new-age demands of multiple segments.
Comparing Top Metal Slip Ring Brands
The metal slip ring market includes several key players, each renowned for their unique offerings and services. This section provides a comparison of some top metal slip ring manufacturers, discussing their strengths and what sets them apart.
Review of Top Metal Slip Ring Brands
No. | Manufacturer | Website |
---|---|---|
1 | Hangzhou Grand Technology | https://www.grandslipring.com/ |
2 | Moog Inc. | https://www.moog.com/ |
3 | Stemmann-Technik | https://www.stemmann.com/en/home |
4 | Schleifring | https://www.schleifring.com/ |
Hangzhou Grand Technology
Hangzhou Grand Technology Co., Ltd. started as a special slip ring manufacturer in 2011. Grown into slip rings, rotary joints, and slip ring assembly experts of today with 6,000 square meter manufacture complex.
Obtained ISO9001, Rosh, CE, and GJB9001B certificates a number of slip rings, rotary joint patents, and proud of our products can meet military grade. Collaborated with universities, institutes, and renowned factories across Asia and Europe including Panasonic, SIEMENS, CSIC, SAMSUNG, HUAWEI, etc.
Moog Inc.
Moog is a leading supplier of high-performance slip rings for various industries, including aerospace. Among their offerings, Moog’s SR Series Slip Rings are designed for the demanding environments of helicopters, excelling in performance, reliability, and customization potential.
Stemmann-Technik
Stemmann-Technik, a part of the Conductix-Wampfler Group, offers a broad range of slip rings, including solutions for helicopters. Their Livietta Slip Ring Assemblies are designed explicitly for harsh and demanding environments in the aviation sector, providing reliable signal and power transmission.
Schleifring
Schleifring is a well-known manufacturer of electromechanical systems, including slip rings customized for various industries. Their Aircraft Slip Rings cater specifically to helicopters, offering robust performance, low wear, and high reliability to meet the challenges of aviation applications.
If you want to know more about other slip ring manufacturers, you can read Top 10 Slip Ring Manufacturers in China, Top 10 Slip Ring Manufacturers In the USA Market 2023, and Top 10 Slip Ring Industry Key Manufacturers 2023.
Factors Influencing Popularity
User Reviews: Customer testimonials and reviews are often a testament to the quality and performance of a product. On this front, both Moog Inc. and Schleifring have garnered positive feedback for their products’ reliability and durability.
Pricing: While pricing often depends on the product’s specifications and customizations, Stemmann-Technik and Cobham have been noted for their competitive pricing without compromising the quality.
Quality: All four brands have differentiated themselves through their emphasis on high-quality products that can withstand the rigors of demanding applications.
After-sales Service: Exceptional after-sales service is another common factor contributing to the popularity of these brands. Customers appreciate their comprehensive service in terms of support, maintenance, and repairs.
While the best brand can depend on the specific requirements of the user, these manufacturers have consistently ranked among the top due to their commitment to quality, innovation, and customer service. Thus, they serve as excellent starting points for those seeking premium-quality metal slip rings.
Conclusion
Metal slip rings are integral components of various systems that require power or data transmission from a stationary to a rotating part. An understanding of their design, selection criteria, and maintenance procedures can significantly enhance their operational efficiency and prolong their lifespan, making this knowledge indispensable for users and enthusiasts alike.
See What We Can Do