This comprehensive guide will help you unravel the intricacies of standard slip rings, their history, structure, working principle, types, roles in varied industries, and future trends.
Introduction to Standard Slip Rings
A standard slip ring, as the term implies, is a standardized version of a rotary electrical interface, also known as a slip ring, rotary electrical joint, swivel, or commutator. It is a device that enables the transmission of power and electrical signals from a stationary to a rotating structure. This process is known as commutation, which often comes with the challenge of managing tangled wires. However, standard slip rings provide an efficient solution to this issue by ensuring a smooth transition of power or signals without tangling wires or cables.
Such a fundamental capability results in a broad array of applications, and hence, standard slip rings play a significant role across various industries. They are integral components found in numerous electromechanical systems within industries such as aerospace, wind energy, manufacturing, automation, defense, and many more. Also, their usage isn’t limited to just commercial and industrial applications; they feature prominently in consumer electronics, helping to drive a more connected world.
Inherently, the design of a standard slip ring is to deliver a high level of performance, reliability, and longevity, making it a preferred choice for numerous applications. These devices precisely control and manipulate the flow of electricity, greatly enhancing the functionality and efficiency of any operating system or equipment in which they are installed.
Understanding the composition, varieties, working principles, and applications of standard slip rings opens a world of opportunities. It paves a pathway to innovate, enhance efficiencies, and drive toward new frontiers of technological advancements.
Historical Background of Standard Slip Rings
The concept of slip rings has a rich history, deeply ingrained in the annals of engineering progression. Often unheralded, these mechanical devices have been silently fueling advancements in technology and industry for centuries.
The early renditions of slip rings emerged in the basic dynamo-generator constructions during the 19th century. A remarkable early example was the Ljungström generator introduced in 1890 by Swedish brothers Birger and Fredrik Ljungström. In its rudimentary form, the slip ring was used to transform generated alternating current to direct current, proving instrumental in the initial development of power generation.
Through the 20th century, as the world witnessed a rapid surge of infrastructural and technological growth, the simplistic slip ring began to morph. With the advent of early flight and burgeoning telecommunications, there was a growing need for improved electrical communication in rotary devices. Engineers of the time made vital enhancements to the materials and design principles behind slip rings, which proved pivotal in meeting these emerging challenges.
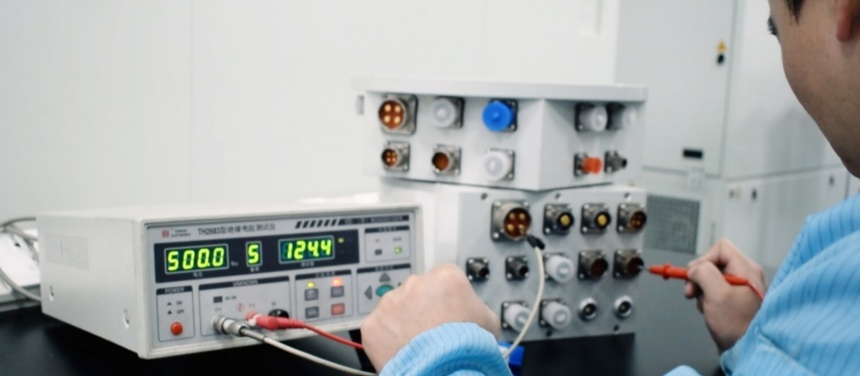
Since then, slip rings have evolved alongside technological and scientific advances. The need for efficient, reliable, and compact power and signal transmission solutions led to the development of the standardized slip ring models we see today.
Driven by incessant innovations, slip rings have continually improved. They transitioned from the basic rotary contacts used in early generator design to more intricate and reliable components that can handle high-speed data transmission. Adding to this, the introduction of contactless or wireless slip rings has addressed many of the limitations of traditional designs, ushering slip ring technology into a new epoch.
From powering the early radio transmissions to enabling high-definition video streams on rotating surveillance cameras, slip rings have undergone several improvements to meet the dynamic demands of industries. Their transformative evolution underscores the adaptability and resilience of these important devices and denotes their unwavering significance in our technological landscape.
Design and Structure of Standard Slip Rings
While often unassuming in appearance, the design and structure of a standard slip ring is a testament to ingenious engineering. These devices are marvels of simplicity and function, seamlessly managing the complex task of transmitting electricity or signals between rotating and stationary parts of a system.
At its core, a standard slip ring comprises three key components: the rotor, the stator, and the brushes. The rotor, as the name suggests, is the rotating part of the slip ring. The stator, on the other hand, is stationary. These two components often feature metallic rings or bands on which ride the third element – the brushes.
The brushes, usually made of a precious metal alloy, maintain a constant electrical connection between the stator and the rotor as the latter rotates. To ensure a long-lasting and efficient contact, these brushes are kept in place with a specific force, enabling them to seamlessly slide over the rotating surface without causing undue wear or heat generation.
While the foundational structure remains the same, the design of slip rings can vary greatly based on the type and application. For instance, a capsule slip ring, best suited for applications where space is a constraint, features a compact, cylindrical design housing concentric rings. In contrast, a through-hole slip ring, typically used in systems where a hollow central shaft is necessary, would feature a larger ring design to accommodate the central opening.
Other design variations include pancake slip rings that use disc-like conductive rings for space-constraint applications; mercury-wetted slip rings that use liquid metal for the conducting media; and wireless slip rings that, while technically not ‘rings’, utilize magnetic fields to transmit data and power without physical contact.
In essence, each type of slip ring is designed with certain specific applications in mind, and the differences in design cater to the unique demands of these applications. Despite this variety, the common goal remains the same across all types – efficient, reliable, and seamless transfer of power or signals across rotating systems.
Working Principle of Standard Slip Rings
At their most basic level, standard slip rings function on a straightforward principle: providing a continuous electrical connection between stationary (stator) and rotating (rotor) components.
This is achieved primarily through the interplay of two key components: the brushes and the rings. In a typical slip ring assembly, the brushes, held in place against the rings, establish a steady electrical connection. As the rotor rotates, the electrical signals or power are transmitted through this connection from the stationary component (stator) to the rotating part (rotor), or vice versa.
In contact-type slip rings, the principle relies heavily on the brushes physically interacting with the rings. This physical contact enables the transmission of electrical signals or power, but it also comes with potential issues around wear and tear, friction-generated heat, and the need for periodic maintenance.
On the other hand, contactless slip rings, also known as wireless slip rings, operate on a slightly different principle. These devices utilize magnetic fields or electric coupling to transmit data and power across the rotating interface, without any physical contact between components. This lack of mechanical contact eliminates issues of wear and extends the life span considerably, making contactless slip rings an attractive option for applications demanding high reliability or those exposed to harsh environments.
Regardless of the type and function, the fundamental principle behind all standard slip rings remains the same. They function as a holistic unit to ensure efficient, continuous transmission of power or electrical signals from a stationary body to a rotating element. Understanding this functioning is key to appreciating their role in various applications and their overall significance in our industrial ecosystem.
Types of Standard Slip Rings
The wide-ranging utility of slip rings is partly a result of their diverse types. Each type is designed with unique features and advantages that cater to particular applications. Here is a quick rundown of some of the most common types:
Capsule Slip Rings
Capsule Slip Rings, also known as miniature slip rings, are designed with compactness and lightweight in mind. They’re used especially in applications where space and weight are at a premium. These slip rings embody a cylindrical shape with concentric rings and are commonly used in CCTV, rotary sensors, medical instruments, robotics, and various compact devices requiring power or signal transmission.
Through-Hole Slip Rings
Through-hole slip Rings, or hollow shaft slip rings, carry a central hole. This design allows cables, shafts, or pneumatic lines to pass through, making them ideal for applications where a central passage is needed, such as wind turbines or radar antennas.
Pancake Slip Rings
Pancake Slip Rings adopt a flat, disc-like design where conductive rings are aligned horizontally. These are useful in applications where length is restricted but a larger diameter is permissible. They find application in areas like cable reels, packaging machines, and rotary tables.
Mercury Wetted Slip Rings
Mercury Wetted Slip Rings, although less common, can offer certain advantages. They use liquid metal as the conducting media, which leads to a nearly infinite life and extremely low electrical noise. However, their application is limited due to the environmental hazards, health risks, and costs associated with mercury.
Wireless Slip Rings
Wireless Slip Rings, also referred to as contactless slip rings, use magnetic fields or inductive coupling to transmit power and signals. This eliminates the mechanical wear associated with physical contact, providing increased reliability and virtually maintenance-free operation. They’re particularly applicable in environments where physical contact is not desirable or feasible, like in explosive or highly sanitary conditions.
Each type of slip ring brings its unique strengths to the table, making it best suited to certain applications over others. Selecting the right type of slip ring is instrumental in ensuring the performance and efficiency of the machines and systems they’re incorporated into.
Standard Slip Ring Technical Specifications and Performance Measure
When considering slip rings for any application, an understanding of their key technical specifications and performance measures is indispensable. These aspects define the limits within which a slip ring operates, and they directly impact its functionality and reliability.
Key Technical Specifications
Current Rating: This indicates the maximum amount of current that a slip ring can safely carry. Exceeding this value could overheat the slip ring and cause damage.
Voltage Rating: This is the maximum voltage that a slip ring can handle. Going beyond this limit can risk electrical breakdowns and potential damage to the device.
Maximum Speed: This defines the highest speed, usually denoted in RPM (rotations per minute), at which the slip ring can function while maintaining its integrity and performance. Superior quality slip rings are designed to function efficiently at higher speeds.
Circuit Number: This denotes the number of independent electrical circuits that a slip ring can support. Applications with complex signal or power requirements often need slip rings with a higher number of circuits.
Contact Material: This refers to the materials used for the ring and brush contacts. The choice of material affects friction, wear, and overall performance of the slip ring. DuPont Vespel, gold alloy, and precious metal contacts are common in many slip rings.
Operating Temperature: This is the range of temperatures within which a slip ring can operate without compromising its function or lifespan. Some slip rings are designed to withstand extreme temperatures for specific industrial applications.
Protection Class: This defines the level of sealing protection against ingress of dust or liquids, often according to the international standards of the IP (Ingress Protection) rating system.
Measuring Performance and Impacting Factors
Many factors can affect the performance of a slip ring. The service life, noise level during operation, operating temperature, and vibration resistance are some of the standard measures used to assess performance.
Service life mainly depends on the wear and tear of the brushes and rings, largely influenced by factors like working speed, load current, and the operating environment. Noise level is a crucial factor in applications where quiet operation is a requirement. It is often related to the design quality and assembly precision of the slip ring.
Operating temperature directly affects the reliability and lifespan of the device. It’s influenced by factors such as load current, the heat dispersal ability of the device, and environmental temperature. Vibration resistance is critical in heavy-duty operations like in wind turbines or marine applications.
Need help with Standard Slip Rings? Fill out the form to get personalized assistance and pricing.
Understanding these technical specifications and performance measures is critical in selecting the correct slip ring for a specific application, and also in ensuring its effective and long-lasting operation once installed.
Standard Slip Ring Applications across Different Industries
Standard slip rings find applications across a wide range of industries, where they facilitate the seamless transmission of power and signals between rotating and stationary components. In this section, we delve into some primary industries where slip rings are employed and explore case studies that showcase their real-world advantages.
Aerospace
In the aerospace industry, slip rings are employed in satellite antennas, guidance systems, and cockpit instrumentation. Rotating systems like gimbal assemblies or antenna stabilization platforms benefit from the long service life and reliable data transfer that slip rings provide.
Case Study: Satellite Antenna Systems
In satellite communication systems, slip rings enable smooth rotation and continuous data transfer in the antenna’s azimuth and elevation axes. This ensures precise tracking of satellites and stable transmission of signals.
Wind Energy
Wind turbines rely on slip rings to transmit power and data between the rotating nacelle and the stationary tower. They also allow for continuous pitch control of turbines’ blades. Long-life, low-maintenance slip rings are particularly valuable because wind turbines often operate in remote and harsh environments.
Case Study: Pitch Control Systems
In wind turbines, the pitch control system determines the blades’ angles and optimizes energy production based on wind conditions. Slip rings allow electrical signals and power to pass seamlessly between the blades and pitch motors, ensuring efficient power generation and protection in adverse weather conditions.
Security and Surveillance (CCTV)
CCTV cameras commonly use slip rings to provide continuous power and data transmission as the cameras pan and rotate. The compact design of capsule slip rings is particularly beneficial in this sector, as several cameras can be deployed in a relatively small space.
Case Study: PTZ Cameras
Pan-tilt-zoom (PTZ) cameras enable 360-degree coverage and have the ability to zoom in on specific regions of interest. Slip rings facilitate the constant data and power transfer necessary for PTZ cameras’ functioning, reducing the risk of operational failure and enhancing security.
Robotics
Robotic arms rely on slip rings to relay real-time control signals and provide power to the various moving components. Slip rings are essential in robots with rotational joints or mechanisms, ensuring seamless communication between actuators, sensors, and control systems.
Case Study: Robotic Arms
Many industrial robots, such as those used in automobile manufacturing, feature multi-axis arms. Slip rings within these robotic arms ensure uninterrupted power and signal transmission, contributing to increased operational efficiency and smooth performance.
These examples underscore the versatility and utility of slip rings across different industries. As technology progresses, slip rings will be pivotal in enabling ever more sophisticated systems and addressing real-world challenges.
Standard Slip Ring Installation, Maintenance, and Troubleshooting
Ensuring a slip ring performs optimally and has a long service life involves proper installation, regular maintenance, and effective troubleshooting of any issues that may arise. Below, we provide a comprehensive guide on how to effectively handle these aspects.
Installation Guide
Step 1: Unpacking: Be sure to handle the slip ring with care during unpacking to avoid any damage. Pay attention to any handling instructions provided by the manufacturer.
Step 2: Placement: Decide the point of installation, and make sure it’s clean and free from any debris. Also, ensure that the area has proper heat dissipation facilities as overheating can reduce the life of the slip ring.
Step 3: Securing: Depending on the type of slip ring, you either secure it with screws/bolts or mount it directly onto a shaft or flange. Ensure the slip ring unit is firmly secured and that no excessive force is applied during this process.
Step 4: Connecting cables: Connect the cables as per the wiring diagram provided by the manufacturer. Extreme care should be taken during this step as incorrect connections can cause severe damage to the slip ring and the associated devices.
Step 5: Post-installation check: Before turning on the device, double-check all connections and clearances to ensure a successful installation.
Maintenance
Routine maintenance of slip rings increases their lifespan and maintains performance levels. Here are a few best practices:
- Inspection: Regularly check for any signs of wear or damage. Particular attention should be paid to the brushes and contact surfaces.
- Cleaning: Keep the slip ring clean and free from dust or debris. Dust can increase electrical resistance, thus reducing performance.
- Lubrication: In the case of certain types of slip rings, periodic lubrication may be required.
Troubleshooting
If the slip ring is not functioning as expected, troubleshooting is needed. Here are a few common problems and potential solutions:
- Poor transmission: This can be due to debris, dust, or oxidation on the contact surface. Cleaning the slip ring might resolve this issue.
- Noise during operation: This may indicate wear or damage to the brushes or rings. Inspect these parts and replace them if necessary.
- Decreased performance in high temperatures: Overheating may be due to a lack of appropriate heat dissipation. Ensure that the cooling system (if any) is functioning properly, and consider adding heat sinks or fans if needed.
By following these installation, maintenance, and troubleshooting best practices, the lifespan and overall performance of the slip ring can be greatly enhanced, delivering effective operation over the long haul.
Standard Slip Ring Safety and Environmental Considerations
The handling and operation of slip rings involve the application of electricity in motion, which creates safety and environmental considerations. It’s imperative to follow safety guidelines and adhere to environmental policies about the use and disposal of such electrical components.
Safety Guidelines
Electrical Safety: Technicians should always ensure that electrical equipment is disconnected or powered down before any maintenance or troubleshooting. Avoid touching surfaces that may still be electrically charged.
Mechanical Safety: Appropriate handling methods should be used during the installation or removal of slip rings to avoid causing any mechanical damage. Technicians should use the correct tools and always follow the manufacturer’s instructions.
Operational Safety: Ensure that the operating area is clear of any debris that might interfere with the moving parts of the slip ring assembly. Regularly inspect the assembly for wear or damage that could compromise its operational integrity.
Environmental Considerations
Recycling and Disposal: End-of-life slip rings often contain materials that can pose an environmental hazard if not disposed of properly. Depending on their construction, they may contain heavy metals or other hazardous materials. As such, they should be recycled at designated facilities, or disposed of by local regulations.
Energy Efficiency: More energy-efficient slip rings can result in significant power savings over time. Technologies like low-resistance brushes and contacts can help to reduce power loss in slip ring assemblies.
Emissions: While slip rings don’t directly emit pollutants, their manufacture and disposal could have an associated environmental impact, including energy use and material waste. Therefore, choosing slip rings from manufacturers with sustainable practices can reduce these environmental effects.
The safety and sustainability of slip ring systems depend largely on user practices and the design and manufacturing policies of the producers. By following safety protocols, as well as selecting and disposing of slip rings responsibly, users can both protect personnel and minimize environmental impacts.
Standard Slip Ring Market Leaders and Their Key Offerings
The global slip ring market features multiple leaders, each bringing unique offerings to meet diverse industry requirements. Here, we present an overview of some leading manufacturers in the standard slip ring market and highlight their key products and unique selling propositions.
No. | Manufacturer | Website |
---|---|---|
1 | Hangzhou Grand Technology | https://www.grandslipring.com/ |
2 | Moog Inc. | https://www.moog.com/ |
3 | Stemmann-Technik | https://www.stemmann.com/en/home |
4 | Schleifring | https://www.schleifring.com/ |
Hangzhou Grand Technology
Hangzhou Grand Technology Co., Ltd. started as a special slip ring manufacturer in 2011. Grown into slip rings, rotary joints, and slip ring assembly experts of today with 6,000 square meter manufacture complex.
Obtained ISO9001, Rosh, CE, and GJB9001B certificates a number of slip rings, rotary joint patents, and proud of our products can meet military grade. Collaborated with universities, institutes, and renowned factories across Asia and Europe including Panasonic, SIEMENS, CSIC, SAMSUNG, HUAWEI, etc.
Moog Inc.
Moog is a leading supplier of high-performance slip rings for various industries, including aerospace. Among their offerings, Moog’s SR Series Slip Rings are designed for the demanding environments of helicopters, excelling in performance, reliability, and customization potential.
Stemmann-Technik
Stemmann-Technik, a part of the Conductix-Wampfler Group, offers a broad range of slip rings, including solutions for helicopters. Their Livietta Slip Ring Assemblies are designed explicitly for harsh and demanding environments in the aviation sector, providing reliable signal and power transmission.
Schleifring
Schleifring is a well-known manufacturer of electromechanical systems, including slip rings customized for various industries. Their Aircraft Slip Rings cater specifically to helicopters, offering robust performance, low wear, and high reliability to meet the challenges of aviation applications.
If you want to know more about other slip ring manufacturers, you can read Top 10 Slip Ring Manufacturers in China, Top 10 Slip Ring Manufacturers In the USA Market 2023, and Top 10 Slip Ring Industry Key Manufacturers 2023.
Each of these companies represents key players in the slip ring industry, offering distinctive products that cater to an array of sectors. It is their continuous innovation and reliable products that set them apart in the industry and provide them with a dominant stance in the market.
Standard Slip Ring: The Future of Slip Rings
The ever-evolving technological landscape is leading to significant advances and opportunities for the slip ring industry. As new trends emerge and novel areas of application are explored, the future of the standard slip ring industry looks both vibrant and promising.
Emerging Trends and Technological Advancements
Miniaturization: As machinery and devices become smaller and more compact, so too do slip rings. The trend towards miniaturization has pushed manufacturers to design slip rings that deliver the necessary performance but in a compact size suitable for installation in smaller equipment.
Increased Connectivity: The Internet of Things (IoT) and the increase in autonomous systems are driving the need for slip rings that can support higher data rates. High-frequency, high-speed data transmission slip rings are becoming increasingly common as a result.
Materials Science: Advancements in materials like graphene and high-temperature superconductors could potentially revolutionize the slip ring industry. Such materials might alter how electricity is transmitted and reduce the wear & tear of existing models.
Future Applications and Developments
Renewable Energy: The deployment of slip rings in wind turbines and other renewable energy equipment is expected to grow. High-performance slip rings will increasingly be needed to ensure reliable power and signal transmission in these systems.
Space Exploration: As nations push further into space, slip rings are critical for facilitating communication and power transfer in spacecraft and rovers. With the private space industry on the rise, exploration missions to the moon, Mars, and possibly beyond, will drive demand for high-functionality slip rings.
Automated and Robotic Systems: In the world of automation and robotics, the role of slip rings is ever-growing. As these systems require continuous power and data transmission, advanced slip rings will increase in demand.
The future of slip rings holds immense possibilities. As technology advances, the slip ring industry will continue to evolve to meet the ever-changing demands of various sectors, paving the way for even more innovative designs and solutions.
Conclusion
The ever-evolving Standard Slip Rings have made tremendous strides over the centuries, and their future appears even brighter. Understanding their types, operation principles, and usage across industries will help one appreciate their ubiquitous presence in our lives. Their story is a testament to human ingenuity and the endless pursuit of technological advancement.
See What We Can Do