This article delves into the realm of high-pressure slip rings, a specialized variant of slip rings designed to operate under high-pressure conditions. It aims to cover the fundamentals, applications, technical specifics, user concerns, and the latest advancements in the field, offering a comprehensive guide for professionals and enthusiasts alike.
Introduction to High-Pressure Slip Rings
In the realm of electrical engineering and mechanical systems, slip rings play a pivotal role in facilitating the transmission of power and data across rotating interfaces. Essentially, slip rings are electromechanical devices that allow for the continuous transfer of electrical signals and currents from a stationary part to a rotating part. This capability is crucial in applications where a rotating structure needs to maintain an electrical connection with a static system, from wind turbines where slip rings transmit power and data from the nacelle to the stationary base, to medical machinery like CT scanners that require data transfer from the rotating part of the machine to the computer.
While the basic concept of slip rings is straightforward, the specific category known as high-pressure slip rings introduces a critical layer of functionality tailored for environments subjected to extreme pressure conditions. High-pressure slip rings are engineered to withstand the rigorous demands of operations where standard slip rings would fail due to intense environmental pressures. These specialized devices incorporate robust sealing and insulation technologies, allowing them to maintain their integrity and performance in high-pressure environments such as deep-sea explorations, oil and gas extraction sites, and aerospace applications.
Another specialized category is the high vacuum RF slip ring, which is designed for use in environments that require both high-frequency data transmission and high vacuum conditions, such as in satellite systems or particle accelerators. The high vacuum RF slip ring shares the same principles of robust sealing and insulation but adds the complexity of maintaining stable signal transfer in vacuum environments, where airless conditions can affect traditional electrical components.
The definition of high-pressure slip rings, thus, extends beyond their fundamental purpose of electrical transmission, fostering a unique niche of applications that operate under conditions where ordinary equipment would succumb to the crushing forces. Their specific role transcends the mere facilitation of power and data transfer; they are integral components that ensure the operational viability and reliability of sophisticated machinery in some of the most challenging and hostile environments on and off the planet. This capability not only highlights the engineering marvel behind high-pressure slip rings but also underscores their indispensable value in pushing the boundaries of exploration, energy production, and high-stakes research.
The Basics of High-Pressure Slip Rings
High-pressure slip rings operate on the foundational principle of standard slip rings, but incorporate certain design enhancements to fare well in environments subjected to extreme pressure. The core function of these devices is to establish uninterrupted electrical connections across rotating platforms, even when the system as a whole is operating under high pressure. They achieve this by using a brush and ring interface where the brush, connected to the stationary part, maintains a continual contact with the rotating ring, to facilitate the transfer of power or signals.
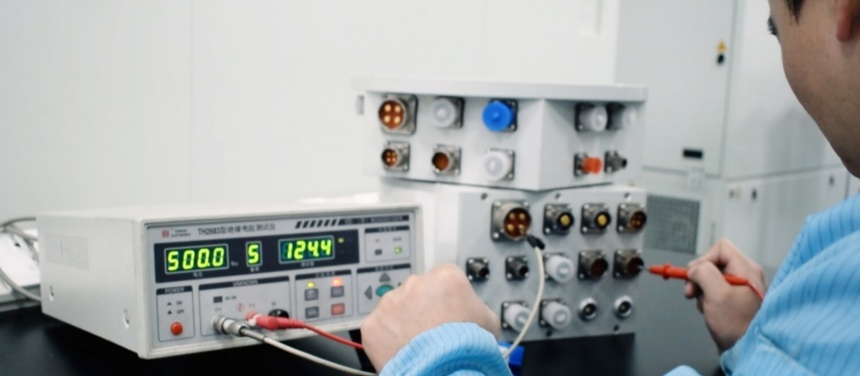
In terms of construction, the choice of materials and components used in high-pressure slip rings is determined by the significant need for durability and resilience. These slip rings typically boast robust metal alloys for housing and contact materials, like gold or silver, to strike a balance between wear resistance and high conductivity. In addition to these robust metals, composite materials may also be used in certain ring designs because of their resistance to stress and lower cost.
A distinguishing feature that sets high-pressure slip rings apart is their focus on advanced sealing and insulation technologies to handle intense pressures. The electrical contacts and rotating components are housed within a sealed unit to prevent damage due to high pressures and to isolate the contacts from the external environment. Special-purpose insulating materials that demonstrate exceptional compressive strength and insulation characteristics are used to prevent electrical shorts, which could be harmful for both the equipment and personnel.
When comparing high-pressure slip rings with their standard counterparts, the key differentiation lies not in the basic operation but in their ability to withstand extreme pressure environments. Standard slip rings, while equally effective in transmitting power and signals, are not designed to maintain their performance under high-pressure conditions, which would cause the materials and components to fail due to deformation or leaks. High-pressure slip rings, on the other hand, are specifically designed and built to remain undeterred by these challenges, ensuring reliable operation where standard slip rings simply cannot survive.
In essence, high-pressure slip rings represent a specialized evolution of the standard slip ring technology. Their advanced design and sophisticated construction allow them to operate effectively in a niche set of applications marked by high-pressure environments, paving the way for advancements in sectors such as deep-sea exploration, oil and gas, and aerospace.
Applications of High-Pressure Slip Rings
High-pressure slip rings are indispensable in various industrial sectors, enabling complex machinery to operate efficiently in environments where pressure and durability are of paramount concern. These dynamic devices are not limited to a singular industry but span across multiple domains that push machinery to extreme operational limits.
In the marine industry, particularly, high-pressure slip rings shine as fundamental components in submersibles and Remotely Operated Vehicles (ROVs). Submersibles, often used for deep-sea exploration and scientific research, rely on these slip rings to power instruments and maintain data transmission to the surface despite the crushing pressures of the ocean depths. ROVs, which perform tasks ranging from underwater welding to resource extraction, make use of high-pressure slip rings to ensure a consistent energy supply and control signals between the operator and the vehicle, allowing for precise maneuvers and real-time data acquisition in the relentless conditions of the seafloor.
Moving to the oil and gas industry, drilling equipment harnesses the power of high-pressure slip rings to sustain critical operations. Deep-earth drilling apparatus and offshore drilling rigs utilize these devices to facilitate the flow of electricity and data transfer across the rotating parts of the drill head assembly even when subjected to both high-pressure and high-temperature conditions that exist thousands of feet below the earth’s surface. These conditions could easily degrade ordinary machinery, but high-pressure slip rings endure, ensuring uninterrupted operations and safety for the drilling platforms that are vital for global energy extraction.
In the domain of aerospace and defense, the role of high-pressure slip rings becomes even more diverse and critical. Whether it’s spacecraft, military jets, missiles, or surveillance systems, each application involves components rotating under considerable atmospheric or combat-incurred pressures. High-pressure slip rings ensure that there are no lapses in communication, power delivery, stability, and control systems, which are critical in high-stakes operations. In spacecraft, for instance, slip rings contribute to the deployment of solar panels and antennae, while on fighter jets, they maintain the functionality of radar and targeting systems, all within intensely pressurized environments.
Through these examples, one can appreciate how high-pressure slip rings carve their uniqueness in each application. They are not simply a generic solution; instead, they are custom-engineered to meet the stringent requirements of each sector. The adoption of high-pressure slip rings speaks to the demand for robust, reliable components capable of withstanding some of the most hostile environments encountered by human-engineered machinery.
High-Pressure Slip Rings: Technical Specifications and Considerations
High-pressure slip rings are designed with specific technical specifications to ensure they remain operational under pressure and can handle the electrical requirements of the system in which they are installed. These parameters determine not only the performance but also the safety and durability of the slip ring in its environment.
The key electrical specifications include current and voltage ratings that the slip ring is designed to transmit. These must be aligned with the power supply and the electrical demand of the rotating system. Exceeding the rated current or voltage can lead to overheating and potential failure of the slip ring. Therefore, careful consideration of these parameters, based on the application requirements, is crucial during the selection process.
Fill out the form to get pricing on our range of high-pressure slip rings.
In addition to these electrical specifications, mechanical factors like pressure tolerance levels and temperature ranges also warrant careful attention. The pressure tolerance level indicates the maximum pressure that the slip ring can withstand within operation without risking damage or compromise in its performance. Typically expressed in units of pressure such as PSI (pounds per square inch) or Pascals, this information is vital in environments with high-pressure like underwater operations or space explorations.
Similarly, the specified temperature range of the high-pressure slip ring declares the maximum and minimum temperatures at which the device can safely operate. This includes considerations for both operating temperature ranges, during active use, and storage temperature ranges, when not in use. High-pressure slip rings used in applications such as drilling equipment or aerospace systems must be resilient to wide temperature variations to ensure reliability.
Another key aspect in selecting a high-pressure slip ring is its compliance with certifications and industry standards. This reflects the device’s adherence to internationally recognized norms for safety, quality, and environmental impacts. Certifications such as ISO (International Organization for Standardization) signify that the product has been manufactured following stringent quality standards, ensuring its reliability. Similarly, compliance with specific industry standards is a testament to the device’s suitability for specialized applications.
In conclusion, not just one, but a combination of several electrical and mechanical specifications along with compliance to regulatory standards govern the selection and application of high-pressure slip rings. These technical considerations ultimately influence the performance, safety, and longevity of the slip ring in its operational environment, reinforcing the necessity of their thorough evaluation.
High-Pressure Slip Rings: User Concerns and Challenges
High-pressure slip rings are crucial in many complex systems where ordinary components cannot survive. However, their deployment comes with several user concerns and challenges that must be addressed to ensure system integrity and operational success.
Durability and reliability under extreme conditions stand as primary concerns for users. They expect these components to perform flawlessly over extended periods despite the high-pressure environments and other extreme working conditions they may face, such as corrosive substances, vibration, and shock loads. Users need assurance that these slip rings will not fail unexpectedly, which could lead to costly downtimes or even catastrophic system failures. Therefore, manufacturers must rigorously test high-pressure slip rings to ensure they meet longevity and reliability standards before they reach the market.
The issue of maintenance and ease of access for repairs is also a pressing concern. High-pressure slip rings are often deployed in areas that are not easily reachable, such as deep-sea equipment, aerospace systems, or sub-surface installations in the oil and gas industry. If a slip ring requires maintenance or repair, the associated costs and logistics can be significant. Hence, users look for slip rings that offer a long maintenance-free operational life or those that are easy to access and repair when necessary, without requiring complete system shutdowns.
Compatibility with various communication and power protocols is another area of user concern. In an increasingly interconnected world, the ability of high-pressure slip rings to handle a variety of signal and power requirements is critical. Users need slip rings that are versatile in their compatibility with different types of data communication protocols and power transmission standards to integrate them into existing systems seamlessly.
Lastly, cost implications and return on investment are always part of the decision-making process. High-pressure slip rings are specialized components and come at a higher cost compared to standard slip rings. Users must evaluate whether the added cost is justified by the performance benefits and longevity provided by these high-end slip rings. They must consider the total cost of ownership, which includes not only the initial investment but also long-term expenses related to maintenance, potential downtimes, and the lifespan of the slip ring. An ideal high-pressure slip ring solution would offer high performance, minimal maintenance, and reasonable cost, leading to a favorable return on investment over time.
In addressing these challenges, users must carefully consider their specific needs and the conditions in which the slip rings will operate. Manufacturers, on their part, should provide clear specifications, maintenance guidelines, and support services to help users make informed decisions and effectively manage these concerns.
High-Pressure Slip Rings: Design and Customization
The deployment of high-pressure slip rings in various industrial applications necessitates advanced design and customization capabilities to meet precise operational demands. This segment of the industry is not one-size-fits-all; the specificity of applications requires tailored approaches in design and manufacturing.
The Necessity for Custom Designs to Meet Specific Application Requirements
Custom designs are crucial due to the myriad of operating environments and technical specifications unique to each application. For instance, a slip ring used in deep-sea exploration faces different challenges, such as saline corrosion and extreme pressure, compared to one used in space, where vacuum conditions and temperature extremes prevail. Customization allows for adjustments in materials, seals, configurations, and electrical properties to ensure that the slip ring not only survives but operates effectively in its intended environment. Tailoring these components to the application’s demands directly influences performance, durability, and overall system reliability.
Case Studies or Examples of Custom Solutions
Deep-Sea Exploration
In one case, a manufacturer was approached to design a slip ring for a submersible vehicle tasked with surveying ocean floors at depths exceeding 10,000 meters. The challenge was twofold: ensuring the slip ring could withstand pressures over 1,000 atmospheres while providing stable power and data transmission.
The solution involved a bespoke design with specialized high-grade materials to resist corrosion, a robust sealing mechanism to prevent water ingress, and a compact, high-density contact design to facilitate numerous power and data channels. The outcome was a highly reliable, pressure-resistant slip ring that enabled the submersible to transmit valuable seabed data back to the surface in real time, opening new avenues for oceanic research.
Aerospace Applications
Another instance involved developing a slip ring for a satellite’s solar array, which required flawless operation in the vacuum of space and thermal extremes ranging from -170°C to 120°C. The custom design focused on minimizing friction and wear in the vacuum environment, using materials that could withstand high doses of space radiation without degrading.
The engineering team deployed advanced ceramics and specialized lubricants for the contacts, coupled with a unique configuration that balanced the load across all contact points, thus ensuring an extended operational lifespan. This design facilitated reliable power transmission to the satellite’s systems, significantly contributing to the mission’s success.
These examples underscore the importance of custom designs in the deployment of high-pressure slip rings across a diverse range of applications. The capacity to tailor each component to meet the exact requirements of its operating environment not only extends the operational life of the machinery it supports but also opens up new possibilities in what can be achieved in challenging and extreme conditions.
Advancements and Trends in High-Pressure Slip Ring Technology
The field of high-pressure slip ring technology is witnessing a period of rapid advancements and evolving trends. These developments are not only enhancing the performance and reliability of slip rings but also pushing the boundaries of their applications. From deep-sea exploration to aerospace and industrial automation, continuous innovation in this area plays a crucial role in the operational success and efficiency of complex systems.
Innovations in Materials and Manufacturing Processes
One of the most significant areas of advancement comes in the form of innovations in materials and manufacturing processes. The industry is moving beyond traditional metal and plastic compounds to incorporate advanced ceramics, high-grade alloys, and composite materials that offer superior properties in terms of strength, durability, and resistance to extreme conditions.
Materials like graphene and carbon nanotubes are being explored for their exceptional electrical, thermal, and mechanical properties. These materials can significantly reduce wear and tear, enhance thermal management, and improve electrical conductivity, thereby increasing the lifespan and reliability of slip rings in high-pressure environments.
Furthermore, additive manufacturing (3D printing) is revolutionizing the way slip rings are produced. This technology allows for complex geometries that were previously impossible or too costly to manufacture, enabling more compact, efficient, and customized designs. This flexibility in manufacturing also accelerates the prototyping process, allowing for rapid testing and iteration of designs to meet specific application requirements.
Integration with Other Technologies
Another notable trend is the integration of high-pressure slip rings with other cutting-edge technologies such as fiber optics and wireless communication systems. The incorporation of fiber optic channels within slip rings enables the transmission of vast amounts of data at high speeds, a crucial requirement for many modern applications including real-time monitoring and control systems.
Wireless communication capabilities are also being integrated, reducing the reliance on physical connections and thus minimizing wear and potential points of failure. This not only improves reliability and data throughput but also simplifies installation and maintenance processes.
Environmental Sustainability Considerations
Environmental sustainability is becoming a central focus in the development and deployment of high-pressure slip ring technology. Manufacturers and users alike are increasingly aware of the environmental impacts of their operations and are seeking ways to minimize their footprint. This has led to innovations aimed at reducing energy consumption and using environmentally friendly materials and manufacturing processes.
Recyclable materials and those with a minimal environmental impact throughout their lifecycle are being prioritized. Moreover, designs are being optimized for efficiency, not only to reduce power consumption but also to decrease material wastage during production. Additionally, some companies are exploring ways to refurbish and recycle old slip rings, further contributing to a reduction in environmental impacts.
These advancements and trends underscore a dynamic and evolving field where continuous innovation is driving improvements in performance, reliability, and environmental sustainability of high-pressure slip rings. As these trends progress, they promise to expand the applications and capabilities of slip ring technologies, fostering new opportunities and solutions across various industries.
Selecting the Right High-Pressure Slip Ring Provider
In the specialized field of high-pressure slip rings, choosing the right provider is crucial. The performance and reliability of slip rings have a direct impact on the overall success and efficiency of the systems they are integrated into. From deep-sea exploration equipment to aerospace systems, the demands placed on these components call for not only high-quality manufacturing but also strong support and customization capabilities from providers.
Criteria for Selecting a Manufacturer or Supplier
Experience and Proven Track Record
A provider’s experience and track record in designing and manufacturing high-pressure slip rings should be a primary criterion. A history of successful projects and satisfied clients points to a deep understanding of the technical challenges and solutions in this niche field. Experienced providers are more likely to have encountered and resolved a range of issues, equipping them with the insights necessary to deliver reliable, high-performance products.
After-sales Support and Warranty
The complexity and critical nature of high-pressure slip rings necessitate robust after-sales support and warranty commitments. Providers should offer comprehensive troubleshooting, repair, and replacement services. A strong warranty indicates confidence in product quality and a commitment to customer satisfaction post-purchase. It’s also indicative of the provider’s readiness to maintain a supportive relationship over the lifespan of their products.
Customization Capabilities
Given the diverse applications of high-pressure slip rings, the ability to customize is essential. Providers must have the technical expertise and manufacturing flexibility to develop bespoke solutions that meet specific operational requirements, ranging from unique environmental conditions to specialized operational functionalities. This capability ensures that the slip ring will integrate seamlessly into the broader system, maximizing performance and reliability.
Tips on Working with Providers for Bespoke Solutions
Define Requirements Clearly
A successful custom solution starts with clear communication. Defining your requirements in detail, including environmental conditions, electrical and data transmission needs, and physical constraints, helps the provider understand your specific challenges and objectives.
Engage in the Design Process
Be prepared to engage closely with the provider’s design and engineering teams. This collaboration can involve reviewing preliminary designs, providing feedback, and perhaps even testing prototypes. Active involvement ensures the final product truly meets your needs and can significantly reduce development time.
Leverage the Provider’s Expertise
High-pressure slip ring providers possess a wealth of knowledge and experience. Don’t hesitate to ask for advice on best practices and for innovative solutions to difficult challenges. Their insights can introduce new possibilities and optimizations that enhance the overall solution.
Plan for the Future
Consider not only your current needs but also potential future requirements. A provider that can scale and adapt solutions as your needs evolve will be a valuable long-term partner, enabling smooth upgrades and expansions with minimal disruptions.
Selecting the right high-pressure slip ring provider is a strategic decision that impacts the performance, reliability, and lifecycle costs of critical equipment and systems. Through careful consideration of a provider’s experience, support commitments, and customization capabilities, and by following strategic tips for collaboration, organizations can secure a partnership that brings lasting benefits.
Conclusion
High-pressure slip rings stand at the crossroads of innovation, offering solutions critical for the success of modern engineering projects. Their evolution and the effort to overcome associated challenges highlight the technology’s significance in pushing the boundaries of what is possible in high-pressure applications.
FAQs about High-Pressure Slip Rings
Q: Can high-pressure slip rings be customized for any application?
A: Yes, most providers offer customization services to tailor slip rings to specific project needs, including adjustments in size, capacity, and pressure ratings.
Q: How do high-pressure slip rings handle data transmission?
A: Apart from power, these slip rings are designed to handle various data protocols, including Ethernet and serial communication, ensuring reliable data transmission even under high pressure.
Q: Are there maintenance-free high-pressure slip rings?
A: While all slip rings require some level of maintenance, advancements in sealing and material technology have significantly extended maintenance intervals, making them nearly maintenance-free.
Q: How do environmental regulations affect high-pressure slip ring design?
A: Environmental considerations are increasingly shaping the design and materials used in high-pressure slip rings, pushing for eco-friendly and sustainable solutions without compromising performance.
Q: What differentiates high-pressure slip rings from standard slip rings?
A: High-pressure slip rings are specifically designed to operate under extreme pressure conditions without compromising performance. Unlike standard slip rings, they are constructed using materials and engineering principles that ensure durability and reliability in environments where traditional slip rings would fail, such as deep underwater or in space vacuum conditions. This includes the use of high-grade materials, advanced sealing techniques, and custom engineering to withstand the specific operational pressures they’ll encounter.
Q: How are high-pressure slip rings customized for specific applications?
A: Customization of high-pressure slip rings involves several considerations to tailor the product to the application’s unique requirements. This process starts with a thorough understanding of the operational environment, including temperature range, pressure levels, and potential exposure to corrosive substances. The electrical requirements, such as the type and amount of data or power to be transmitted, also play a crucial role. Based on these parameters, slip rings can be customized in terms of materials, sealing methods, configurations, and even integration with additional technologies like fiber optics or wireless communication to ensure optimal performance.
Q: Can high-pressure slip rings support the transmission of both power and data?
A: Yes, high-pressure slip rings can be engineered to transmit both power and data simultaneously. These hybrid slip rings are equipped with specialized channels designed for electrical power transmission and data communication, including high-speed signals. The integration of fiber optic technology into the slip ring assembly is a common approach for data channels, offering high-speed, high-bandwidth communication capabilities alongside traditional power transmission.
Q: What maintenance is required for high-pressure slip rings?
A: While high-pressure slip rings are designed for durability and longevity, regular maintenance is still essential to ensure optimal performance. Maintenance routines typically involve visual inspections for wear and damage, cleaning of contacts and surfaces to prevent build-up of contaminants, and testing of electrical functionality to detect any degradation in performance early on. The specific maintenance requirements can vary depending on the operational environment and usage, with harsher conditions necessitating more frequent inspections and care.
Q: How does environmental sustainability factor into the design and operation of high-pressure slip rings?
A: Environmental sustainability is increasingly prioritized in the design and operation of high-pressure slip rings. This involves selecting materials and manufacturing processes with lower environmental impact, designing for energy efficiency, and ensuring the slip rings are durable and repairable to prolong their service life and reduce waste. Providers may also explore recycling programs for end-of-life components. These efforts contribute to a reduced ecological footprint while maintaining the high performance expected from these critical components.
See What We Can Do